Rotational disk dampers find applications in a variety of
mechanical systems. In industrial machinery, such as conveyor
systems, they are used to control the rotation of pulleys. This
ensures that the conveyor belt moves smoothly, preventing sudden
starts and stops that could cause damage to the conveyed materials
or the machinery itself. In some types of printing presses,
rotational disk dampers are employed to regulate the rotation of
the printing cylinders, enabling precise control over the printing
process and resulting in high - quality prints.
Rotary dampers operate on the principle of fluid viscosity or
magnetic - field - induced resistance. In a fluid - based rotary
damper, a viscous fluid, often silicone oil, is enclosed within a
chamber. When the damper experiences a rotational force, a piston
or vane within the chamber moves through the fluid. The viscosity
of the fluid resists this movement, creating a damping effect. The
damping force can be adjusted by changing the viscosity of the
fluid, the size of the piston or vane, or the design of the fluid -
flow channels within the chamber.
In magnetic - field - based rotary dampers, a magnetorheological
fluid is used. This fluid changes its viscosity in the presence of
a magnetic field. By adjusting the strength of the magnetic field,
the damping force can be precisely controlled. This type of damper
offers a high level of adaptability, as the damping characteristics
can be modified in real - time, making it suitable for applications
where the damping requirements may vary.
Rotary dampers are highly versatile and find applications in
numerous industries. In the automotive industry, they are used in
steering systems to provide a smooth and controlled feel to the
driver. The bidirectional functionality of some rotary dampers
allows for damping in both left - hand and right - hand turns,
enhancing the safety and comfort of driving. In furniture, such as
swivel chairs and adjustable tables, rotary dampers enable smooth
and controlled rotation, improving the user experience. In consumer
electronics, like laptop lids and tablet covers, rotary dampers
provide a soft - close mechanism, protecting the delicate
components inside and adding a touch of elegance to the product.

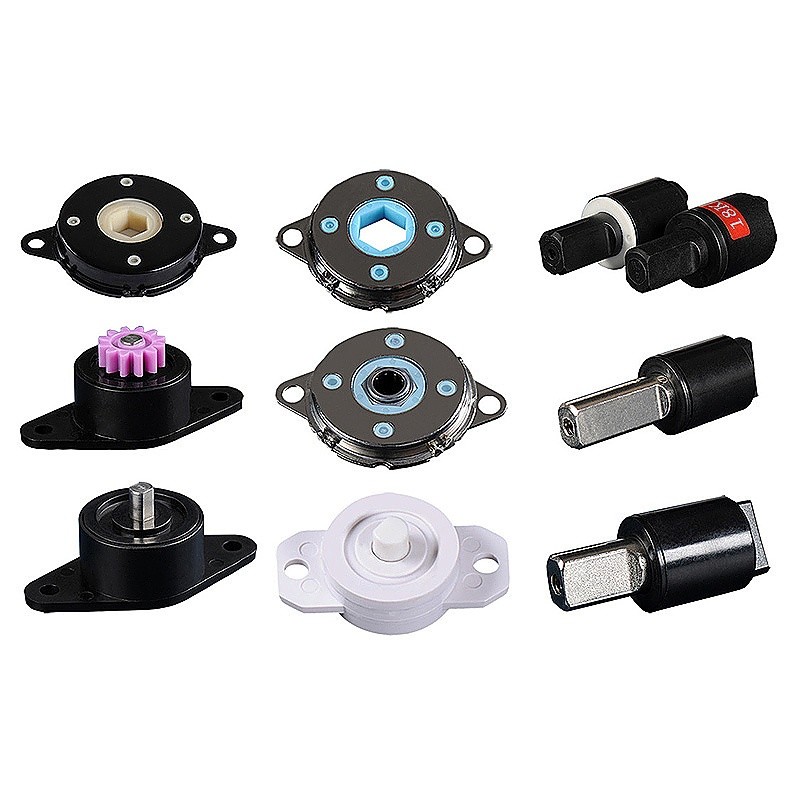
Shock absorbers are specifically designed to absorb and dissipate
the energy of sudden shocks or impacts. They typically consist of a
piston moving within a cylinder filled with hydraulic fluid or gas.
When a shock is applied, such as a vehicle hitting a pothole or a
machine experiencing a sudden impact, the piston compresses the
fluid or gas in the cylinder. The resistance of the fluid or gas to
compression absorbs the shock energy, converting it into heat
energy, which is then dissipated.
The design of shock absorbers can vary depending on the
application. In automotive suspension systems, shock absorbers are
often paired with springs. The springs support the weight of the
vehicle, while the shock absorbers control the movement of the
springs, preventing excessive bouncing and ensuring a smooth ride.
In industrial machinery, shock absorbers may be designed to protect
delicate components from the shockwaves generated during operations
such as metal stamping or heavy - duty equipment starting and
stopping.
In the automotive industry, shock absorbers are a critical
component of the suspension system, directly impacting ride comfort
and handling. They help to keep the tires in contact with the road
surface, improving traction and stability. In construction
equipment, shock absorbers are used to protect the operator's cab
from the vibrations and shocks generated during excavation,
grading, or other heavy - duty tasks. In the aerospace industry,
shock absorbers are employed in landing gear systems to cushion the
impact during takeoff and landing, ensuring the safety of the
aircraft and its passengers.
All three types of dampers - rotational disk dampers, rotary
dampers, and shock absorbers - are designed to dissipate energy and
control motion. They play a vital role in enhancing the
performance, safety, and durability of mechanical systems.
Additionally, they are all engineered using carefully selected
materials and manufacturing processes to ensure reliable operation
under different conditions.
The main differences lie in their working principles and the nature
of the forces they are designed to handle. Rotational disk dampers
primarily deal with rotational forces and rely on friction between
disks for damping. Rotary dampers can operate based on fluid
viscosity or magnetic - field - induced resistance and are more
focused on controlling rotational motion in a wide range of
applications. Shock absorbers, on the other hand, are specifically
designed to handle sudden, high - energy impacts and are commonly
used in applications where protecting against shocks is the primary
goal, such as in vehicle suspensions and industrial machinery.

Rotational disk dampers, rotary dampers, and shock absorbers are
essential components in mechanical engineering, each with its own
unique characteristics and applications. Whether it's controlling
the rotation of industrial machinery, providing a smooth driving
experience in automotive systems, or protecting against sudden
impacts in construction and aerospace applications, these dampers
play a crucial role. Understanding their working principles,
applications, and differences can help engineers and designers make
informed decisions when selecting the appropriate damper for a
given mechanical system. If you are involved in mechanical design,
manufacturing, or improvement, considering the use of these dampers
can significantly enhance the performance and reliability of your
products. Reach out to our team of experts to explore how these
dampers can be tailored to your specific requirements and take your
mechanical systems to the next level.